Service
MatriX provides its international customer base with installation & training, software and hardware services as well as regular maintenance support for its installed X-ray inspection machine base. MatriX' integrated lifecycle service approach minimizes the total costs of ownership by securing stable uptimes, a fast ROI and an extended lifetime for our AXI equipment.
Service Support Worldwide Locations MatriX Service Line
+49 89 2000 33 88 77
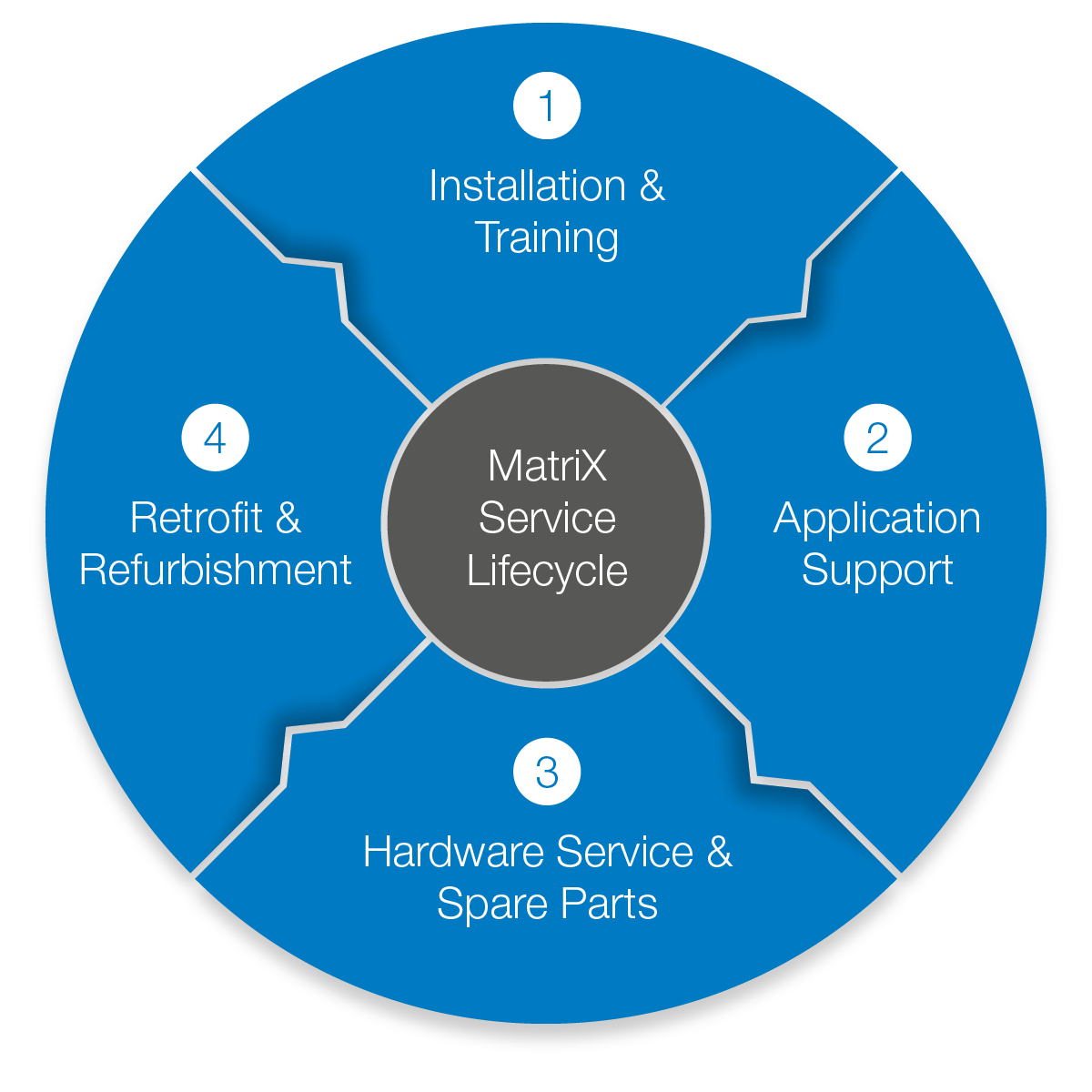
Our customer focused service and maintenance approach guarantees a constant use of the AXI equipment in large scale series productions. As part of our service package, MatriX engineering team provides support in terms of customization of the purchased AXI hardware and MIPS software and latest product configuration requirements. In combination with our different upgrades MatriX ensures flexible utilisation of the purchased AXI equipment and helps to increase sustainably non-defected product yields as well as overall efficiency.
Installation services, staff and operator trainings as well as production bring-up support services are being provided in connection with each AXI/NDT system sale. Extended application and operator trainings are available upon request.
In addition, MatriX offers regular operator trainings as part of an annual general maintenance visit during years 2-4 of the machine operation.
- Operator Training
- Maintenance Training Basic and Advanced
- Application Training Basic and Advanced
MatriX Technologies offers regular hardware maintenance, software services/upgrades, as well as regional spare part support via its regional affiliates and service centres in order to assure extended lifetimes and latest inspection technology upgrades.
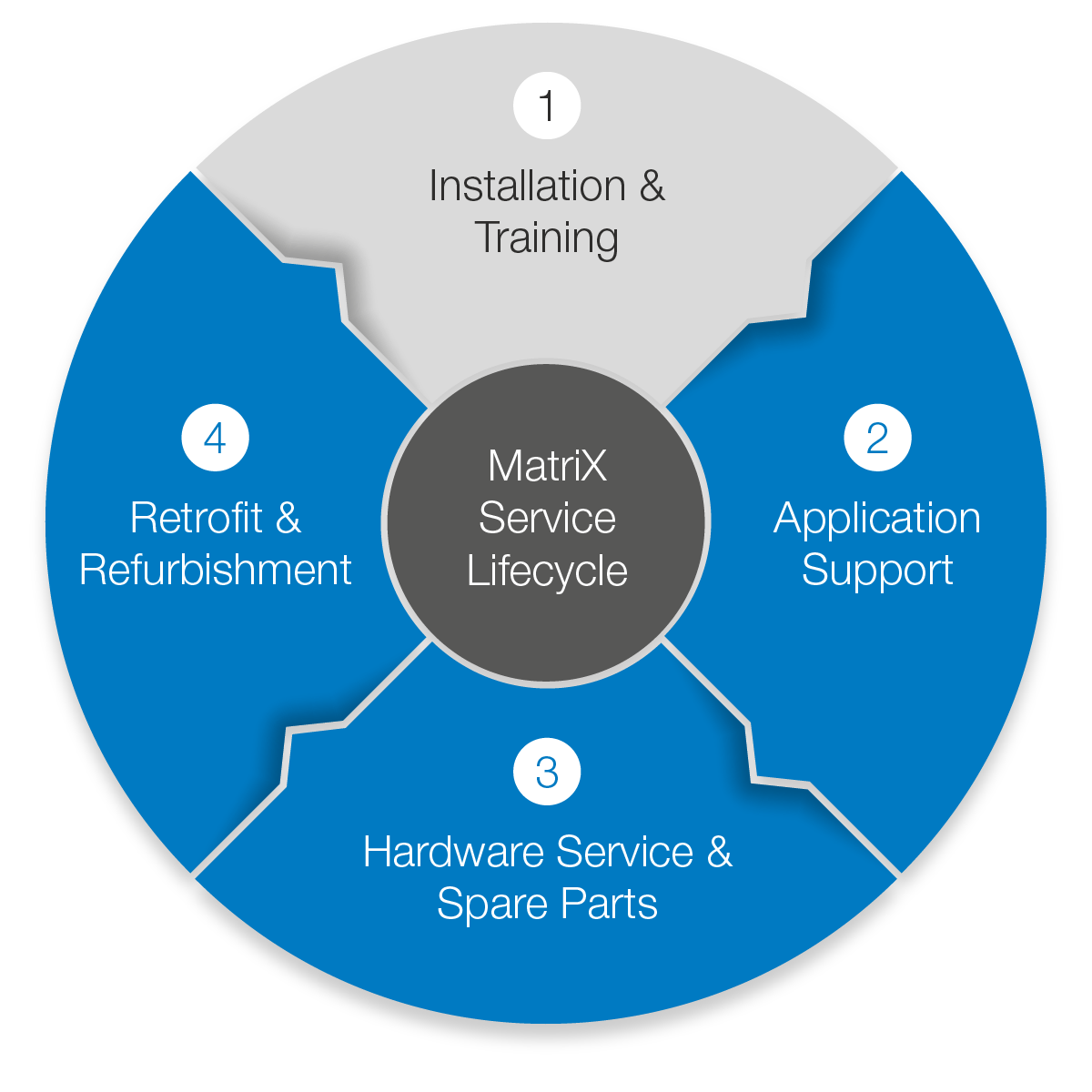
- Permanent software remote support
- New MIPS Software upgrade/licenses
- MIPS Software service (algorithm and model updates)
- Customer application support
- New product application programming
- On-site/production yield improvements
- Software & Application services are available as modular offerings in different service package types (base, advanced and premium)
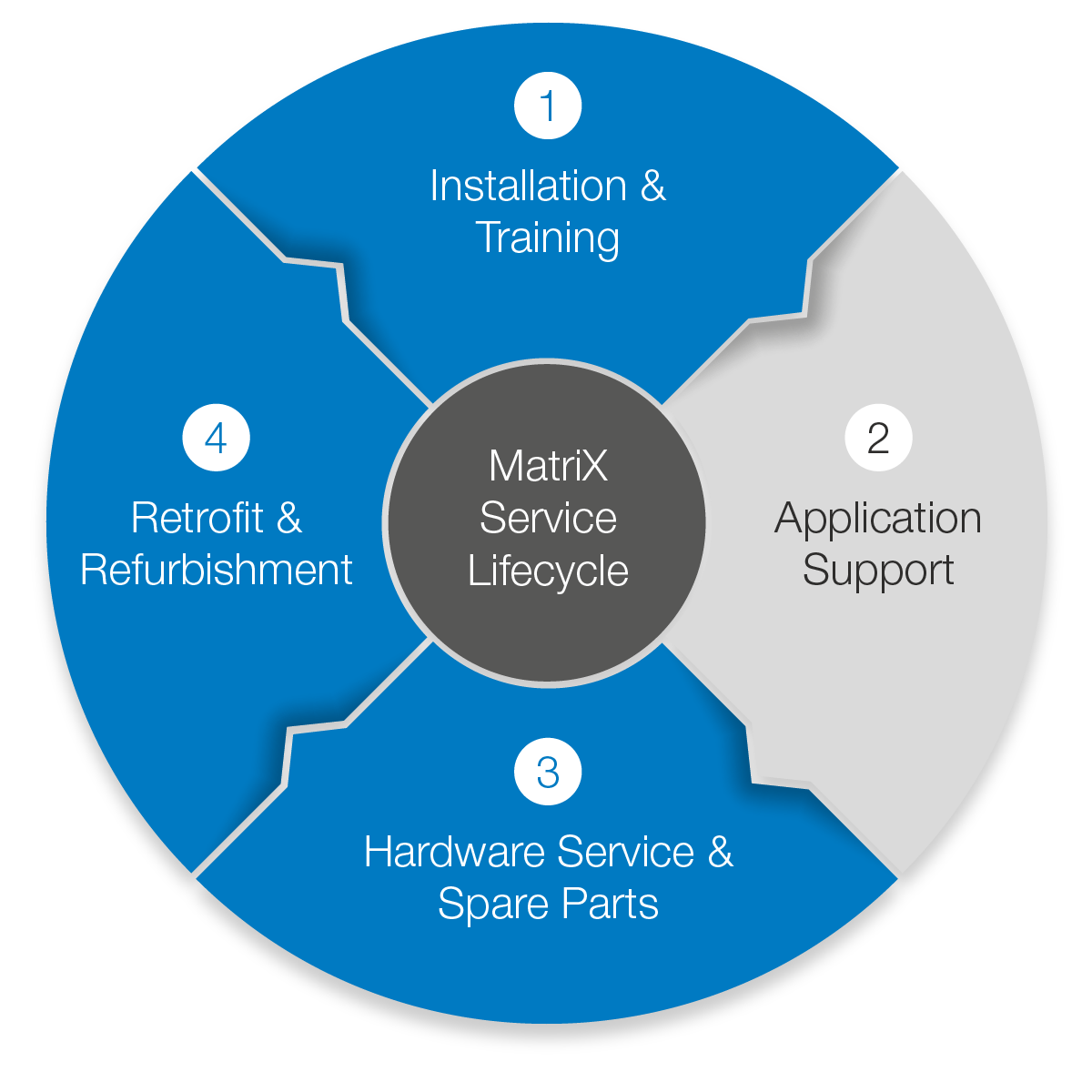
Maintenance hardware services for MatriX inspection systems
- Machine repairs
- Annual hardware maintenance visit (on-site)
- Remote hardware services and hotline support: 12 hours / 5 days up to 24 hours / 7 days per week depending on service package
- Guaranteed on-site response time <48h
- Hardware telephone service
- Emergency shipment preparation <24h
- Annual radiation surveys according to FDA national radiation safety guidelines – certification – North America (US and Mexico)
- Annual tube filter surveys
- Regional spare-part support and warehousing structure at MatriX USA (San Diego, USA), MatriX Inspection Systems (Singapore) and MatriX (Suzhou) Trading Co. Ltd. (China)
- Hardware services are available as modular offerings in different service package types (base, advanced and premium)
Spare Parts Support
- Spare parts supply for MatriX system series include x-ray tubes, image components (detectors, image intensifiers & camera), motion and other electromechanical parts among others
- Spare part kits (level 0/level 1/level 2) for MatriX’ MX 3600 and X2 series available upon request
- Our regional spare-part warehousing structure in Germany, Hungary, US, Singapore and China ensures short lead times for urgent spare part shipment
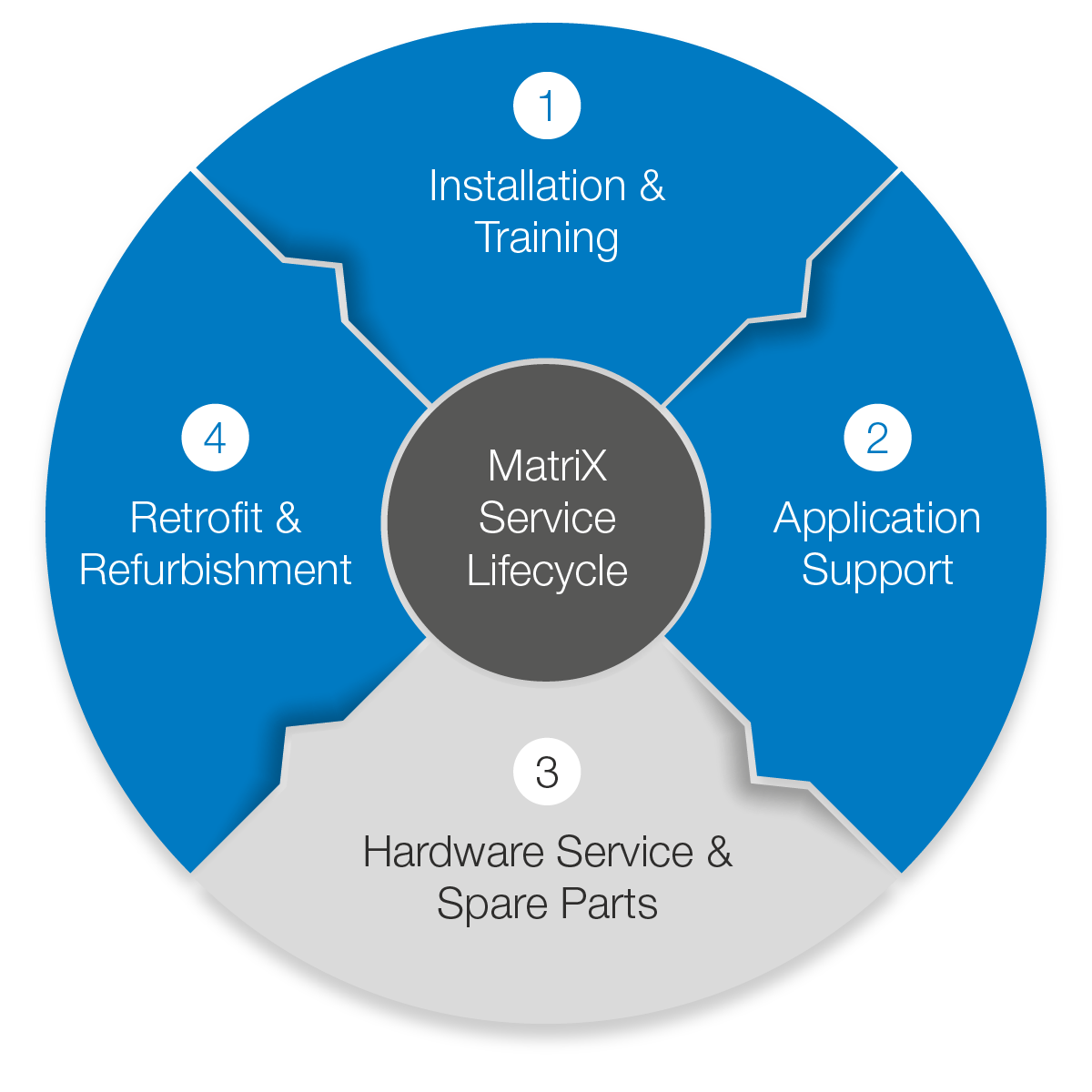
MatriX refurbishment offerings include complete or basic hardware and software upgrades for your installed AXI equipment base in order to:
- Assure a longterm and extended use of your AXI inspection equipment within series production
- Provide you with the opportunity to ugrade your AXI system with the latest state-of-the-art image technology, detector & motion settings
- Adapt your purchased AXI equipment hardware/software to new product applications or new production lines
All provided AXI equipment retrofit options are based on individual customer needs and budgets and immedtiately pay-off against an extended lifetime, increased machine efficiency and material quality.
Complete refurbishment package
- Complete hardware refurbishment and overhaul of the machine after i.e. 5-6 years of use within 24/7 series production
- Exchange of imaging parts (x-ray tube, detector etc.) and other electromechanical parts included
- Adaption of latest MIPS software upgrade
- Complete machine refurbishment will be conducted off-site at the nearest MatriX facility in the US, Asia (China, Singapore) or Europe by MatriX engineering staff
- An AXI loaner can be provided upon request in order to prevent disruption of series production during the refurbishment action
Basic refurbishment
- Basic hardware refurbishment and overhaul of the machine
- Basic machine refurbishment can be conducted on-site (customer’s facility)
Trade-in/recycle options
Should you be interested to purchase a new MatriX AXI inspection system in order to i.e. replace an old MatriX AXI machine within your production line, MatriX is offering to recycle your old machine (trade-in) against a discount or credit on the new machine price. Alternatively, a retrofitted machine can be provided against the old machine subject to availabilities and customer budgets.
AXI systems currently included in the trade-in program:
- X2
- X2.5D
- MX 3600
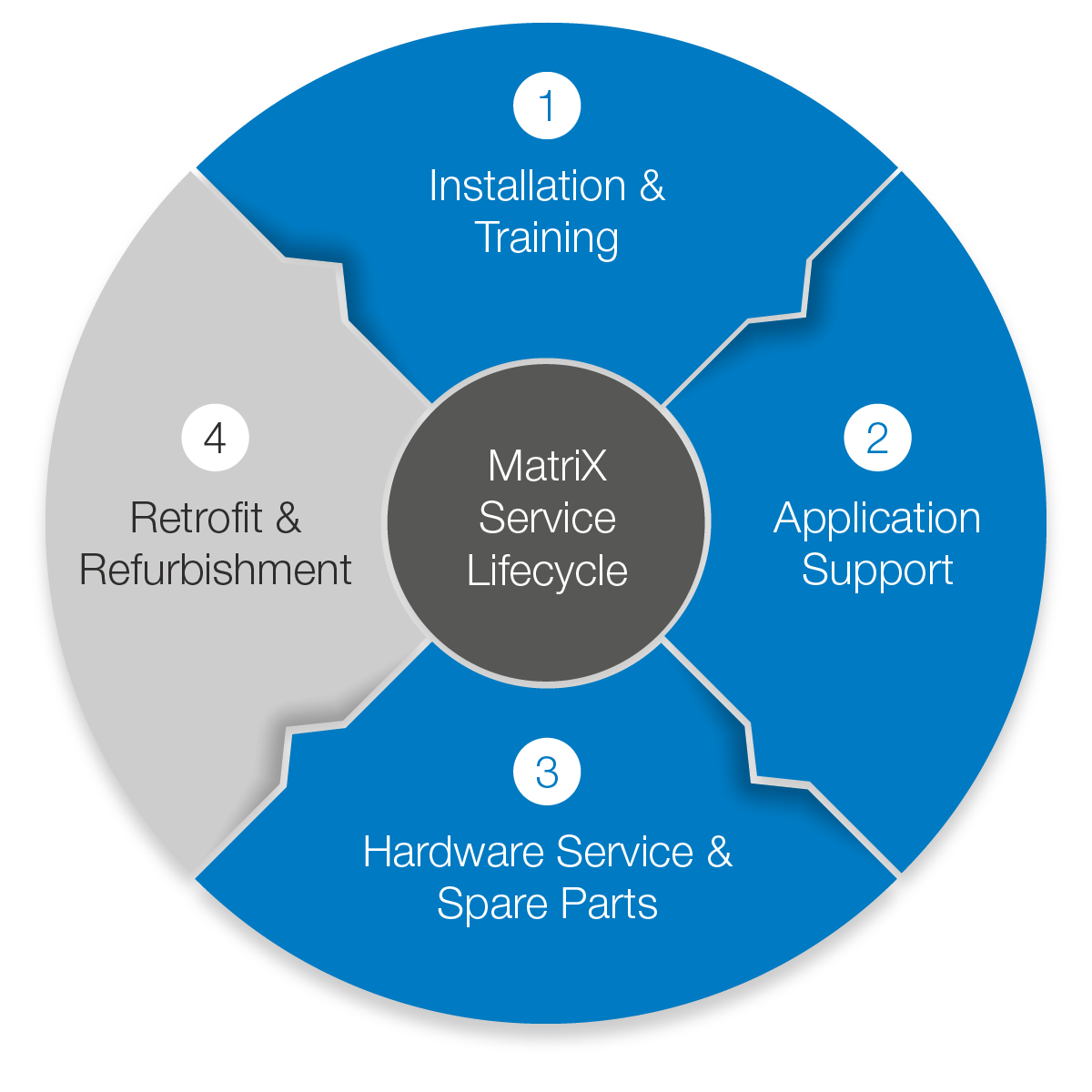
For any technical questions regarding your installed MatriX X-ray system or a general service/spare part request, the central MatriX Service Line is your direct connection to us.
MatriX Service Line +49-89 2000 33 88 77
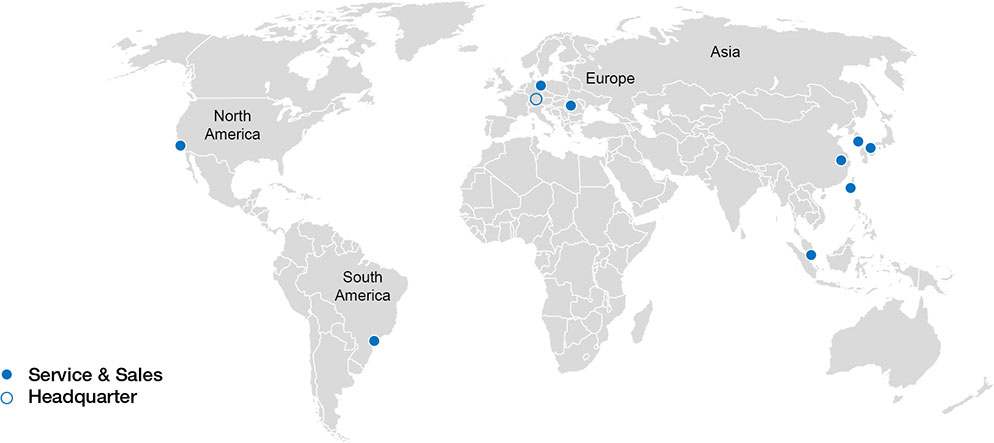